
Crafting Melt Blown Textiles
The most recent
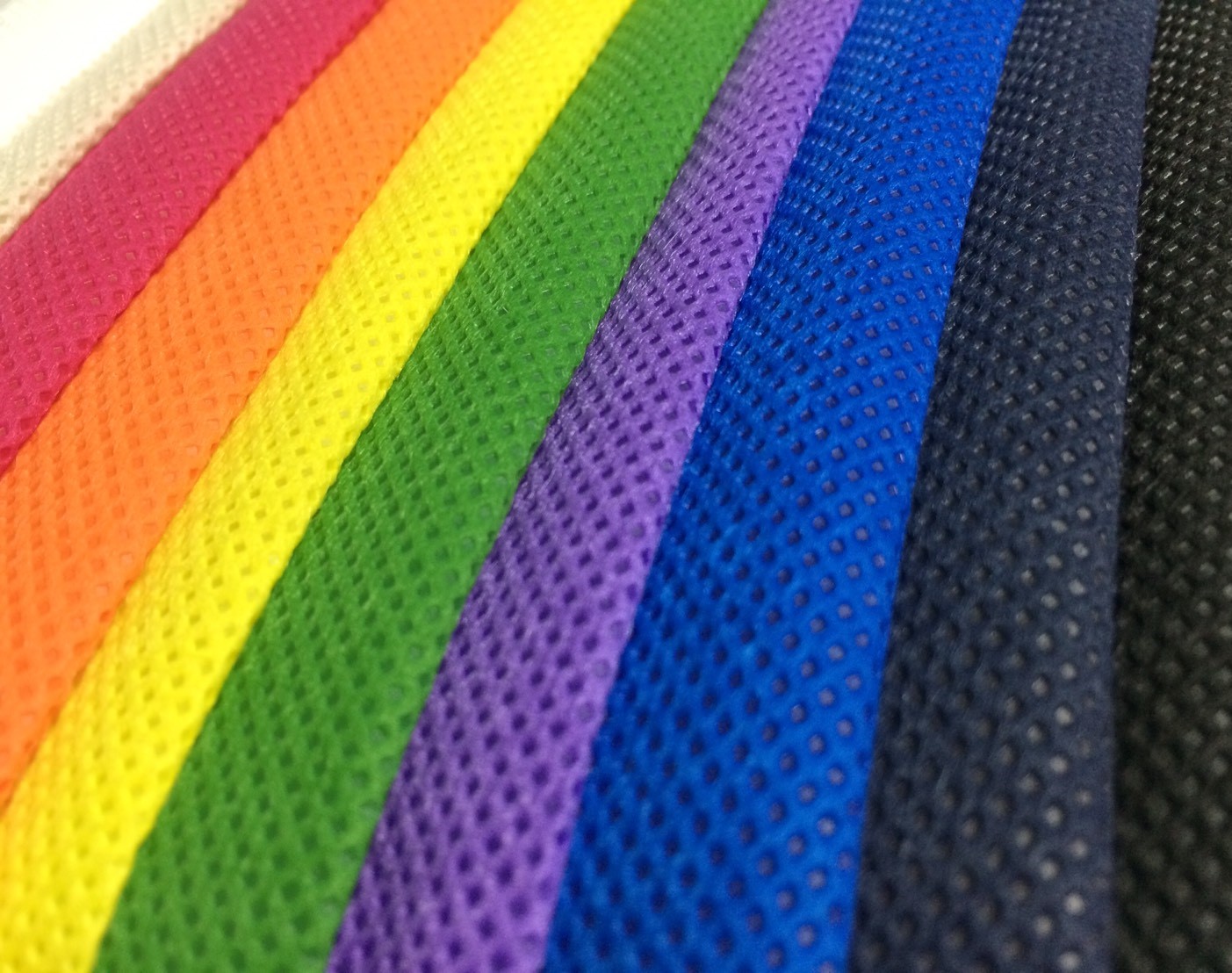
Everything Need to ...
1/16/2024Spunbond fabric is one of the non-woven fabrics made from polypropylene fibers. Due to its positive features and advantages

Hydrophilic Fabric R...
12/5/2023In the quest to combat water scarcity, innovative solutions like fog harvesting have emerged as promising alternatives
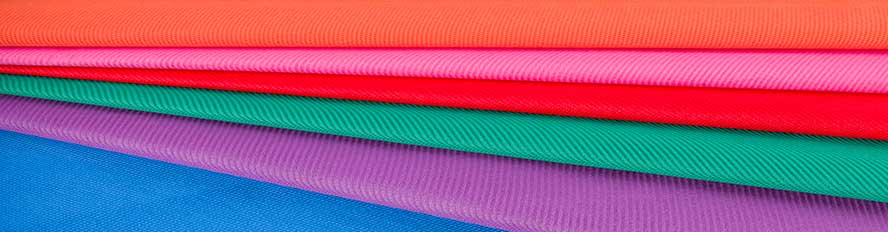
Hydrophilic Fabric
10/4/2023 Given the importance of hygiene and adherence to safety principles in places like hospitals, manufacturers have aimed to produce products that are particularly valuable and effective in this area. Hydrophilic fabric is one of those products designed for this purpose
The most visited
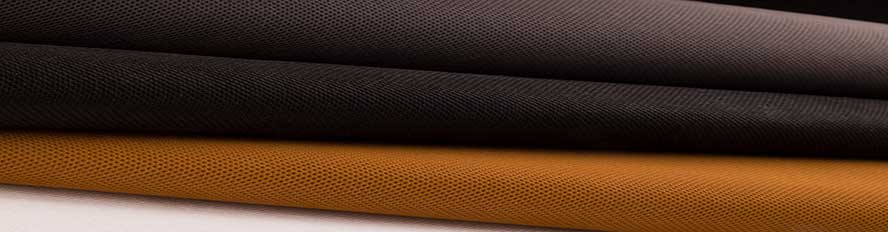
Where to Buy Spunbon...
9/30/2023Spunbond fabrics belong to a category of non-woven textiles made from polypropylene. Unlike conventional fabrics constructed with warp and weft, spunbond materials
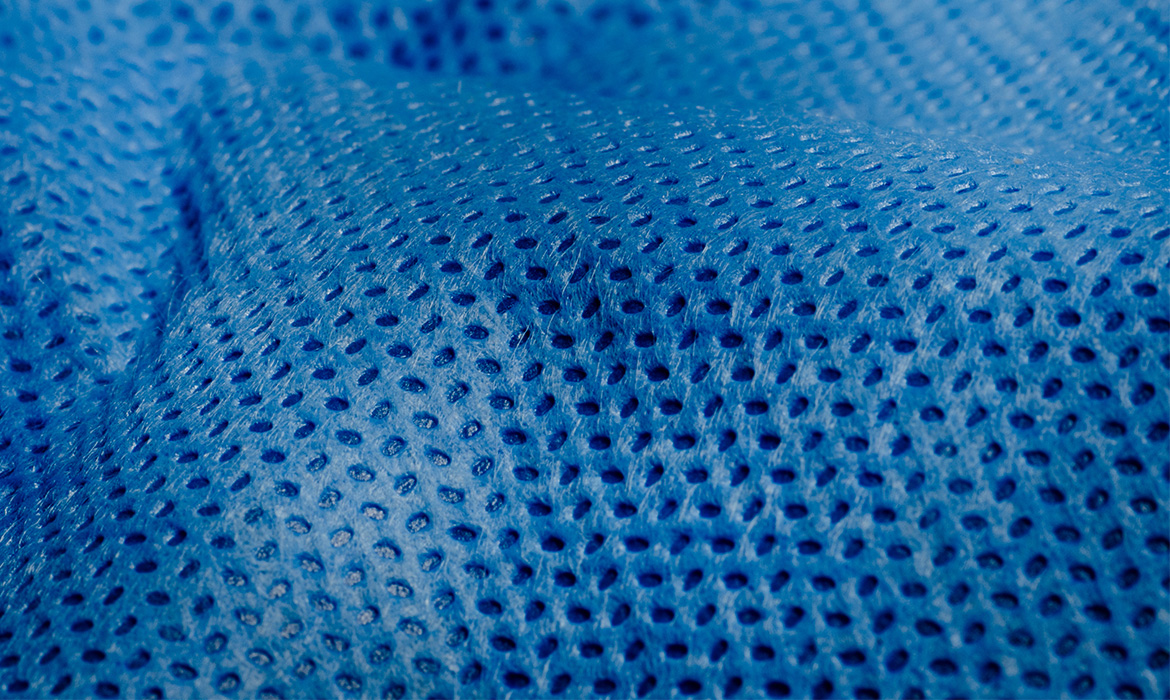
What is Spunbond
10/2/2023One of the most captivating, functional, and widely-used fabrics in the domestic market is the spunbond fabric. This fabric plays a significant role in the production of industrial products due to its unique characteristics.
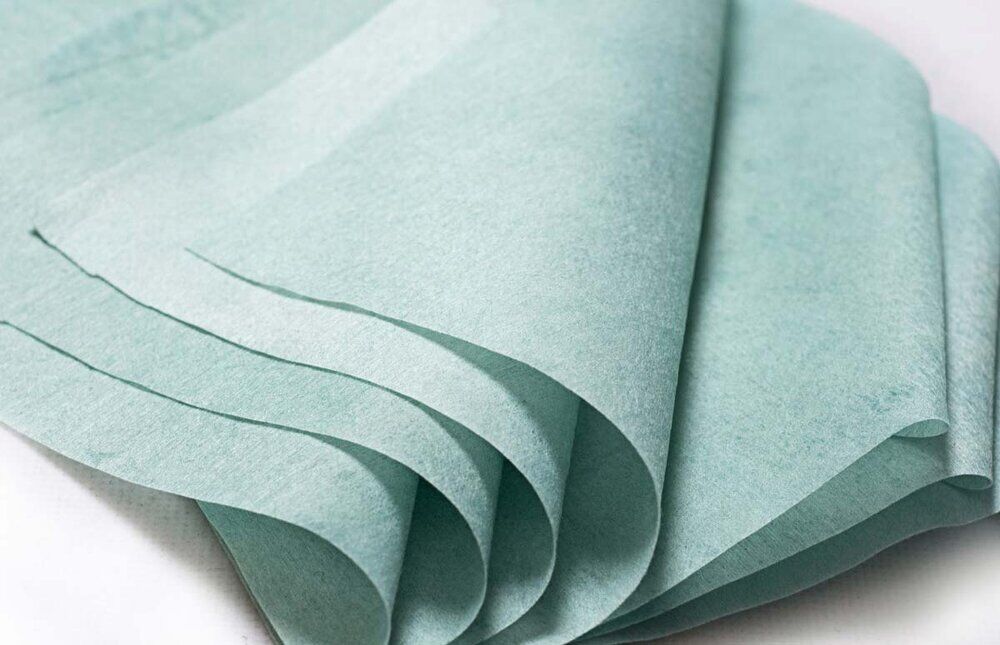
Crafting Melt Blown ...
9/30/2023Melt blown textiles have emerged as one of the most sought-after materials, gaining prominence especially in the healthcare field
subscribe to newsletter
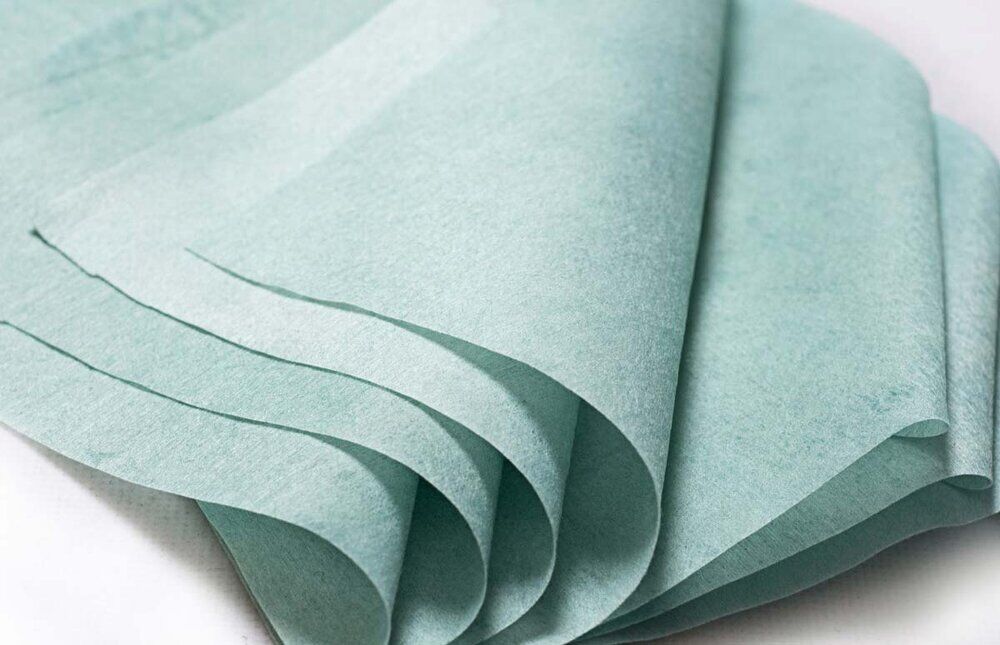
Crafting Melt Blown Textiles
9/30/2023
Melt blown textiles have emerged as one of the most sought-after materials, gaining prominence especially in the healthcare field. This material has gained traction due to its distinctive attributes and benefits. Within the textile realm, there are various manufacturing methods, and the melt blowing technique stands out. If this piques your interest, keep reading.
The Art of Melt Blown Creation
The term "Melt Blown", often shortened to "MB", signifies a unique process that sets it apart from conventional textile crafting techniques. Intriguingly, the foundational concept of this method can be likened to how a cotton candy machine operates, albeit with a touch of modern technological flair. The melt blown process unfolds as:
• This webbed structure is then compressed between two heated rollers.
The end product of the melt blown technique, commonly known as melt blown textile, belongs to the non-woven fabric family. Essentially, it comprises irregular threads with thickness varying from 1 to 5 microns. This key feature lends the melt blown textile its remarkable barrier qualities. Due to these properties, melt blown textiles find multiple uses, with its primary role being in filtration. Its configuration, akin to paper, acts as a filter, trapping microorganisms and oils.
Exploits of Melt Blown Textiles
Some noteworthy applications of melt blown textiles include:
Identifying Quality Meltblown Fabric Methods
Water Resistance of the Mask The ability of the mask to resist water offers insights into the meltblown fabric's quality. A standout trait of meltblown is its impermeability to liquids. To test this, introduce some water inside the mask. If water seeps through, it indicates the absence of meltblown fabric. Another approach is to pour water inside and then drain it. If the mask remains dry with no moisture traces, it confirms the presence of a meltblown layer. However, if moisture is detected, it suggests that the mask production didn't employ meltblown fabric or fibers.
Light Transmission Through the Mask For this evaluation, darken the surroundings completely. Then, illuminate the room using a flashlight or candle. Hold the mask close to this light (around 10 centimeters) and assess the light's appearance beneath the mask. If the light appears diffused, it suggests the mask contains meltblown fabric. Conversely, if you can clearly identify the light source, the mask probably lacks meltblown material.
Mask's Combustibility Cut the mask into two, preferably from the center. Expose this central section to a mild flame. If it burns easily, it suggests the mask doesn't conform to quality standards and lacks meltblown fabric. It's noteworthy that while meltblown fabric might degrade under heat, it doesn't ignite or catch flames.
Mask's Ability to Attract Fine Particles Shred a piece of paper towel and scatter the bits on a flat surface. Using the side straps, hover the mask's exterior close to these shreds. If the mask attracts the paper fragments, it suggests its compliance with quality standards and its fabrication using meltblown fabric.
Mask's Flame Extinguishing Capability Don the mask and ignite a candle or matchstick. Position it around 20 centimeters from your face and blow powerfully towards it. If the flame remains unaffected, it reinforces that the mask is of desired quality, made with meltblown fabric.
Spray Penetration Through the Mask Acquire any spray, say an air freshener, and dispense its content onto the inner layer of the mask. If the spray doesn't permeate to the mask's opposite side, it emphasizes the inclusion of a meltblown layer, promising effective filtration.
Start a conversation
Hello ! Click on a member below and chat.